Understanding Precise Injection Mould Supply in the Metal Fabrication Industry
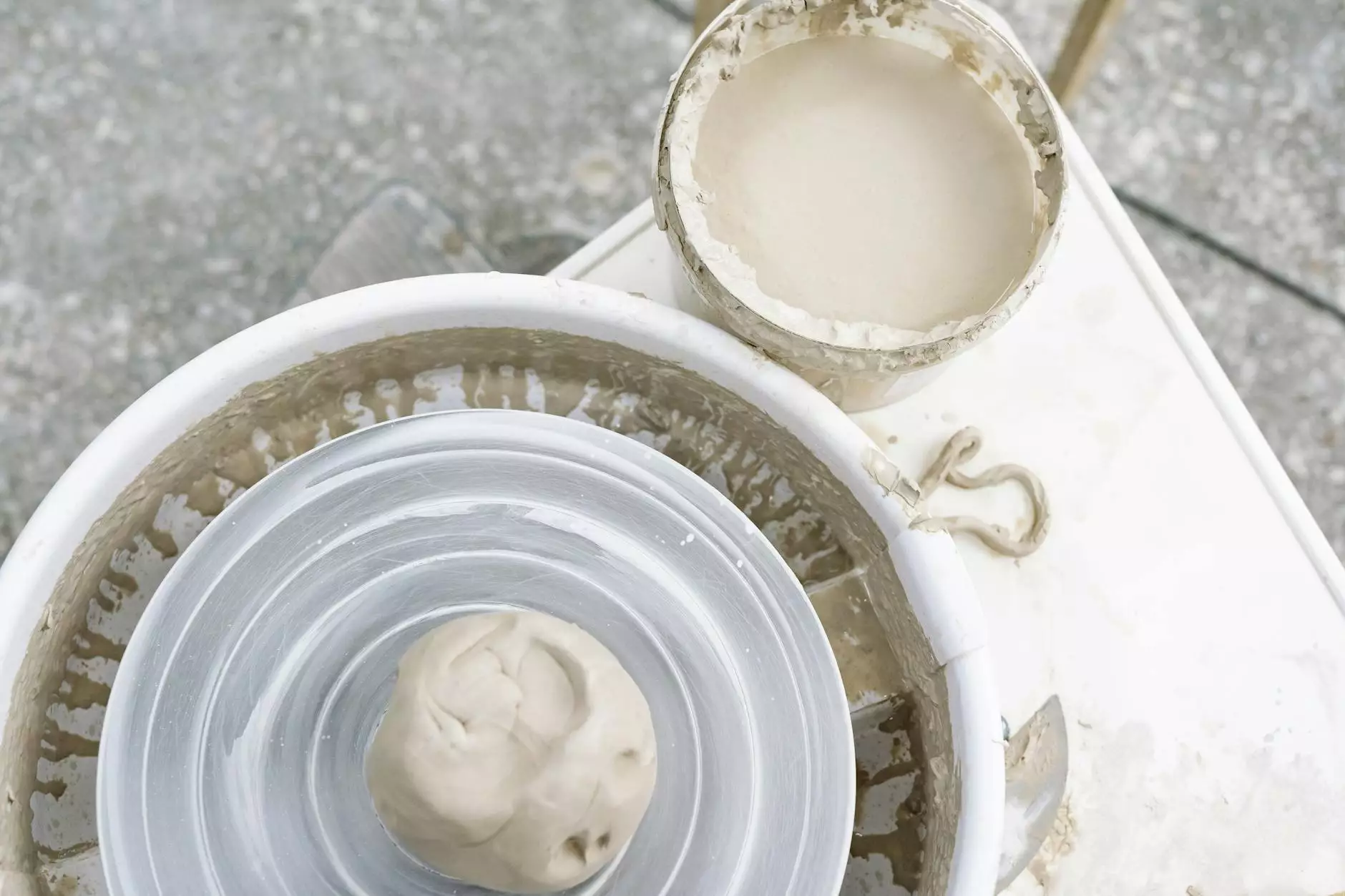
The world of metal fabrication is constantly evolving, driven by the need for precision, quality, and efficiency. One of the critical components that facilitate these requirements in modern manufacturing is precise injection mould supply. This article delves deep into the significance of this process, the technologies involved, and its impact on various industries. By the end of this exploration, you will have a comprehensive understanding of why precise injection moulding is an essential asset in the realm of metal fabrication.
What is Injection Moulding?
Injection moulding is a manufacturing process commonly used for producing parts by injecting molten material into a mould. This technique is widely utilized across various businesses, particularly in the production of both plastic and metal components. The process can be broken down into several key stages:
- Material Selection: Depending on the application, manufacturers choose the appropriate material, which can range from thermoplastics to metals.
- Heating: The selected material is heated to a molten state to prepare it for injection.
- Injection: The molten material is injected into a pre-designed mould at high pressure.
- Cooling: Once injected, the material cools and solidifies in the mould.
- Demoulding: After cooling, the final product is demoulded and inspected for quality.
The Importance of Precise Injection Mould Supply
In the landscape of metal fabrication, the importance of precise injection mould supply cannot be overstated. Here are some reasons why this technique is vital:
1. Consistency in Quality
Precision in injection moulding ensures that each part manufactured is uniform and meets the required specifications. This is crucial in industries such as automotive, aerospace, and electronics, where every component must operate flawlessly within specified tolerances.
2. Cost Efficiency
By utilizing precise injection moulding techniques, manufacturers can produce parts more quickly and at a lower cost. The efficiency of moulding reduces the wastage of materials and energy, contributing to lower overall production costs, which can be passed on to consumers.
3. Enhanced Durability
Products created using high-quality injection moulds tend to have superior mechanical properties, making them more durable and long-lasting. This reliability is essential in applications that demand rigorous performance and safety standards.
Advancements in Injection Moulding Technology
The field of injection moulding is witnessing rapid technological advancements that enhance precision and efficiency. Key advancements include:
- 3D Printing: This technology allows for rapid prototyping of moulds, enabling quicker iterations and modifications before mass production.
- IoT Integration: Smart manufacturing practices are emerging, with IoT-enabled machines providing real-time data on production status, thus enhancing process optimization.
- Use of Advanced Materials: New materials that can withstand higher temperatures and pressures are being explored, opening new avenues for moulding metals more effectively.
Common Applications of Precise Injection Mould Supply
The applications of precise injection mould supply span various industries, showcasing its versatility and importance. Some of the primary sectors include:
Aerospace
The aerospace industry demands high precision and quality assurance in every component, as the slightest deviation can lead to catastrophic failures. Injection moulding ensures that critical parts such as engine components and structural elements meet stringent safety standards.
Automotive
In the automotive sector, manufacturers rely on injection moulding for interior fittings, engine parts, and other essential components that must withstand harsh conditions while providing aesthetic appeal.
Electronics
The electronics industry uses injection moulding to produce intricate housings and components that require precision engineering to ensure proper fit and function.
Medical Devices
Medical device manufacturing is highly regulated, necessitating precision in both functionality and sterility. Injection moulding is employed for producing devices like surgical instruments, diagnostics tools, and drug delivery systems.