Transforming Manufacturing: The Importance of Lathe Turning Parts in Metal Fabrication
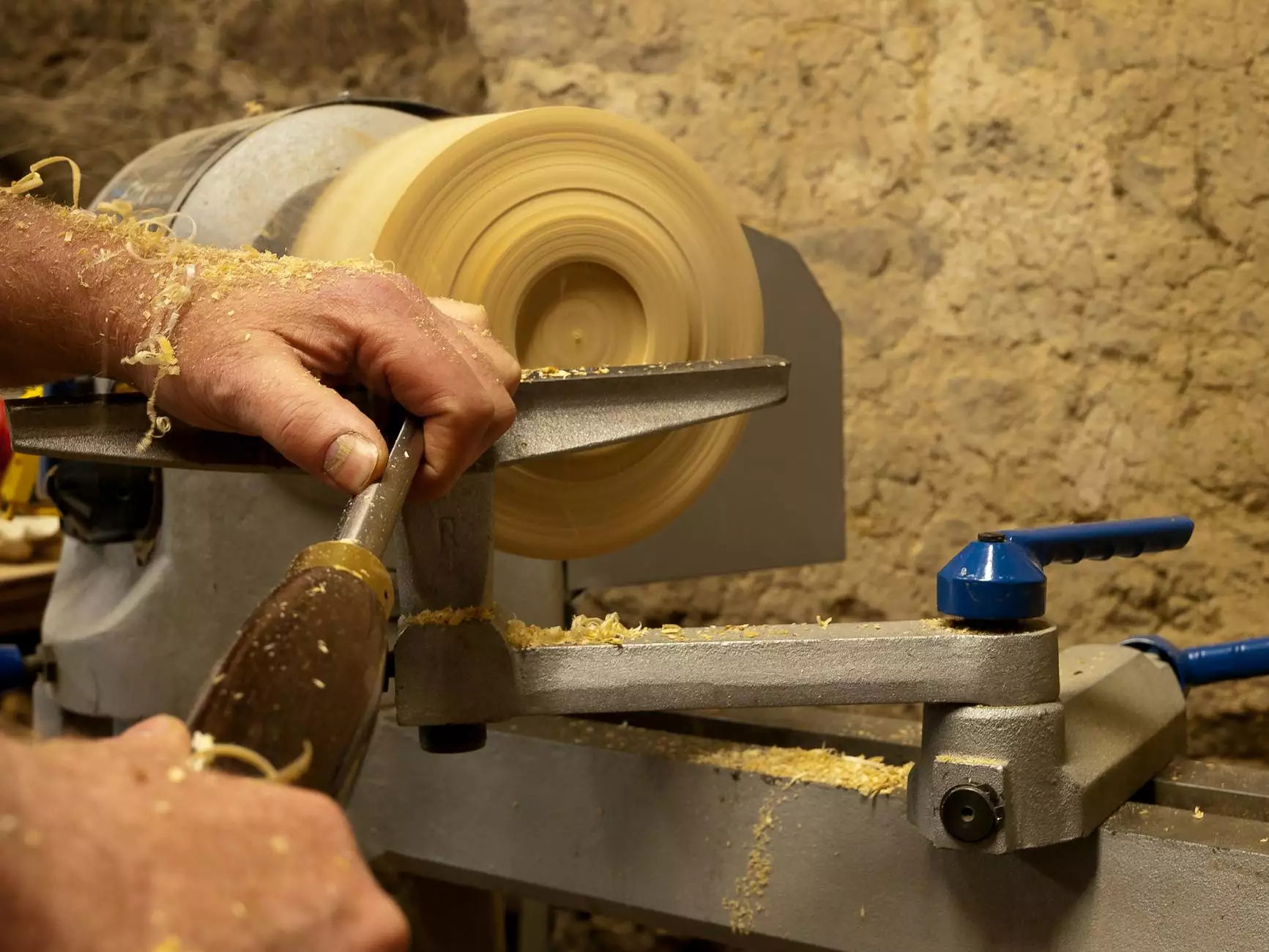
In the evolving landscape of modern manufacturing, lathe turning parts factories play a pivotal role in producing high-quality, precision-engineered components that are vital to various industries. From automotive to aerospace and beyond, these factories leverage advanced technology and skilled craftsmanship to meet the ever-growing demands for precision components. In this article, we delve deep into the significance of lathe turning parts, the processes involved in their production, and the benefits of choosing a reputable factory like DeepMould.net.
Understanding Lathe Turning Parts
Lathe turning is a manufacturing process whereby a rotating workpiece is shaped and formed through the use of a cutting tool. This process allows for the creation of cylindrical parts, as well as complex geometries that require precise tolerances. The benefits of lathe turning are numerous, ranging from efficiency to the ability to produce a wide array of parts.
Key Characteristics of Lathe Turning Parts
- Precision: Components produced through lathe turning are known for their high accuracy and tight tolerances.
- Versatility: This process can produce various shapes and sizes, from simple to complex designs.
- Efficiency: Automated lathes can quickly produce large volumes of parts, significantly improving production times.
- Material Compatibility: Lathe turning can be performed on a variety of materials, including metals, plastics, and composites.
The Lathe Turning Process
The production of lathe turning parts involves a sequence of carefully orchestrated steps. Understanding this process is crucial for businesses looking to optimize their manufacturing capabilities.
1. Material Selection
The first step in the lathe turning process is selecting the appropriate material. Factors such as strength, weight, and corrosion resistance play a critical role in this decision. Common materials used in lathe turning include:
- Aluminum
- Steel
- Brass
- Plastic
2. Designing the Part
Once the material has been chosen, the next step involves designing the part. This typically involves:
- Creating detailed CAD (Computer-Aided Design) models.
- Defining tolerances and specifications to ensure precision.
- Collaborating with engineers to optimize the design for manufacturability.
3. Setting Up the CNC Lathe
After the design process, setting up a CNC (Computer Numerical Control) lathe is crucial. This includes loading the material, programming the CNC machine, and configuring tools for cutting.
4. Machining Process
During this phase, the CNC lathe rotates the workpiece while the cutting tool shapes it according to the programmed specifications. This process can include various operations such as:
- Turning: Removing material to produce the cylindrical shape.
- Facing: Creating a flat face on the end of a part.
- Drilling: Creating holes in the part for assembly.
5. Finishing Operations
After the primary machining is complete, finishing operations may be conducted to enhance the part’s appearance and performance. These can include:
- Polishing: Improving surface smoothness and aesthetics.
- Anodizing: Providing a protective coating for aluminum parts.
- Heat Treatment: Adjusting the mechanical properties of the material.
Advantages of Choosing the Right Lathe Turning Parts Factory
Selecting a reliable and experienced lathe turning parts factory is crucial for ensuring the quality and performance of your components. Here are some of the key advantages:
1. Quality Assurance
Reputable factories adhere to strict quality control standards. At DeepMould.net, we implement rigorous testing procedures to ensure every part meets the exact specifications. This commitment to quality translates into fewer defects and enhanced reliability for your products.
2. Expertise and Experience
Factories with significant experience in lathe turning bring a wealth of knowledge to the table. This expertise not only aids in producing high-quality parts but also in providing valuable recommendations during the design phase. Leveraging the experience of seasoned professionals can lead to improved product designs that are optimized for manufacturing.
3. Advanced Technology
Modern lathe turning parts factories utilize state-of-the-art technology. CNC machinery, automation, and real-time monitoring systems enhance precision and efficiency. By choosing a factory that invests in the latest technology, you can benefit from faster turnaround times and reduced production costs.
4. Customization Capabilities
One of the standout features of lathe turning is the ability to produce customized parts. At DeepMould.net, we specialize in creating tailored solutions that meet the unique requirements of our clients, allowing you to innovate and differentiate your products in the market.
5. Scalability
As your business grows, so do your manufacturing needs. A skilled lathe turning parts factory can accommodate increased production volumes without compromising quality. This scalability ensures you meet market demands without interruption.
Cost Considerations in Lathe Turning Manufacturing
When engaging with a lathe turning parts factory, understanding the cost structure involved is essential for budgeting and financial planning. Several factors can influence the cost of manufacturing:
1. Material Costs
The choice of materials can significantly impact production costs. Metals like aluminum and brass might be cheaper than specialty alloys. Always consider the trade-offs between cost and the required material properties.
2. Complexity of Design
Parts with complex geometries will require more time and resources to produce, leading to higher costs. Simplifying designs without sacrificing functionality can help in reducing production expenses.
3. Production Volume
Higher production volumes often lead to lower per-unit costs due to economies of scale. However, the setup costs for CNC machines can be significant, making it crucial to determine the appropriate volume for your projects.
Environmental Impact and Sustainability in Lathe Turning
As industries evolve, a growing emphasis is being placed on environmental sustainability. Lathe turning parts factories are no exception. Here are some of the ways reputable factories, including DeepMould.net, are addressing environmental concerns:
1. Waste Reduction
Modern CNC lathes are designed to minimize waste through precise machining. Factories are also exploring methods to recycle scrap material, further reducing their environmental footprint.
2. Energy Efficiency
Investing in energy-efficient machinery and processes not only reduces operational costs but also minimizes the factory's carbon footprint. This commitment to sustainability is becoming increasingly important in the eyes of consumers.
3. Sustainable Practices
Incorporating sustainable practices throughout the manufacturing process helps factories operate responsibly. This includes responsible sourcing of materials, reducing emissions, and adhering to environmental regulations.
Conclusion: The Future of Lathe Turning Parts Manufacturing
As we move forward into a more technology-driven era, the demand for precision-engineered components will only continue to grow. Lathe turning parts factories like DeepMould.net are at the forefront of this revolution, providing the expertise, technology, and commitment to quality necessary to excel in today's competitive marketplace.
Businesses seeking reliable suppliers for lathe turned parts can trust reputable factories that prioritize innovation, quality, and sustainability. By making informed choices, companies will not only meet their manufacturing needs but also support the development of sustainable practices that are essential for the future of manufacturing.